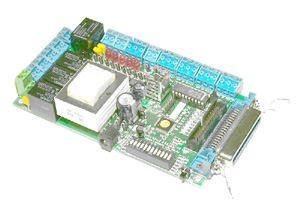
Model PMDX-120
Parallel Port Accessory Module
The PMDX-120 has now transitioned to legacy product status.
It is still possible to special order them but they are not recommended for new
designs. OEMs and those needing replacements should
contact us via email for price and availability quotations.
The PMDX-126 is recommended to users seeking an replacement for the
PMDX-120 in new designs.
Click on image for larger view
The PMDX-120 is an accessory sub-system for small CNC machines using stepper motors or
step-servos driven from the parallel printer port of a personal computer. It can be used
with software such as MACH1, Master5, CNCPRO, EMC, TurboCNC, MaxNC (step/dir version),
DANCAD, and probably many others.
It is ideal for use with Gecko, Compumotor, or other motor drivers that accept step and
direction inputs. It offers support for all pins of the parallel port and allows for
isolation and protection of the parallel port on your computer. Dip switches provide
settings for pinout selection, signal inversion, pulse conditioning, and debug/exercise
modes.
New version with alternate low voltage power input and 5VDC output.
PMDX-120 Parallel Port Accessory Module Features
Breakout board feature comparison table.
General:
- On board power supply operates from 120 VAC via screw terminal strip or 7 to 9 VAC via
a 2.1 mm coaxial power jack. The on board power system provides power to feed
opto-isolated inputs of stepper motor drivers and an accessory +5 volt output for encoders
or external low power devices. It also provides isolated power for sensing contact
closures for status inputs.
- LED "power on" indicator shows presence of input power.
- Pluggable screw terminal strips for connections to motor drivers, relay outputs, and
switch inputs.
PC Parallel Port:
- Buffers signals to/from the PC parallel port. Protects PC from damage. Filters noise.
- Allows use of all 8 data bits, 4 control outputs and 5 status inputs.
- Centronics cable connector uses standard PC printer cable.
- Support for optional ribbon cable to remote 25-pin D connector.
Input Status Signals:
- Inputs are opto-isolated and accept contact closure switches or open-collector sensor
outputs.
- LED status indicators for each input show when switches are closed.
- DIP switch settable polarity control for each input makes testing limit switch inputs
easier.
- Over-voltage protection tolerates direct application of 110VAC to switch inputs without
damage to your computer or the PMDX-120 board.
- Special input to accept "Fault" signal from Gecko step-servo drivers or other
low current sources.
Relay Contact Outputs:
- Isolated, normally open, "dry circuit", electromechanical relay contact
outputs.
- Contacts rated for up to 10 Amps at 125 VAC, 5 Amps at 230 VAC, or 5 Amps at 50 VDC.
- LED status indicators show when relays are on.
- MOV surge arrestors protect relay contacts from arcing.
Motor Step/Direction:
- Independent connectors for 4 axes of step and direction signals.
- Jumper selectable common reference can be either Ground or +5VDC as is often used for
motor drivers with opto-isolated inputs for step and direction.
- User replaceable buffer chip on step and direction outputs.
- DIP switch selectable pinout mapping of data bits to step and direction outputs.
Supports EMC, Master5, TurboCNC, MaxNC, TAIG, CNCPro, DanCAM and many others without
building custom cables.
- DIP switch setting controls the polarity of the step pulse outputs.
- Can optionally regenerate step pulses to uniform width (lengthens short
pulses from PC).
- Ability to latch the direction signal on rising or falling edge of input step pulse,
thus providing extra hold time for direction signal outputs.
- All step and direction signal processing is in hardware logic, no timing distortion
from processing delays.
- Motor activity LED shows presence of step pulses.
Diagnostic Features:
- Allows you to operate motors without a PC connected and test hardware before
configuring software.
- Three diagnostic modes provide single step, run while button pressed, run repeating
square pattern.
Special Notes:
- The PMDX-120 does not support a "charge pump" like that offered by the Mach
software.
- Use with the PMDX-106 spindle controller requires utilizing one pair of axis step and
direction signals as the Direction and PWM signals for the PMDX-106 because the extra
controls signals on a PMDX-120 are relay output only.
Note: The step and direction signals
used to run this board as a real time CNC device require precise timing. These
signals are normally provided by a personal computer motherboard with an onboard
parallel port, a parallel port interface card plugged into a motherboard with
ISA, PCI, or PCI-Express slots, or by an external device such as the
SmoothStepper.
You cannot use a USB to printer adapter because it will alter critical timing of
CNC control signals.
Documentation and Other Useful Files
Download Manual in PDF format here (revision 1.6, 732 KB).
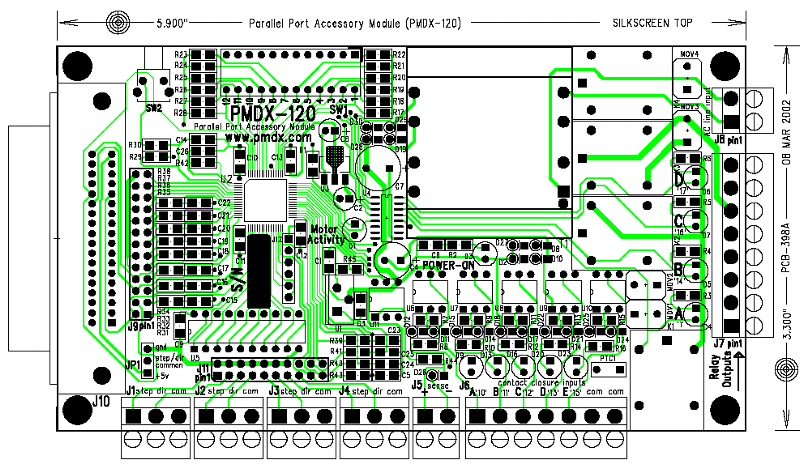
Board layout image with silk-screen legends
A good tutorial on parallel port interfacing can be found HERE
|